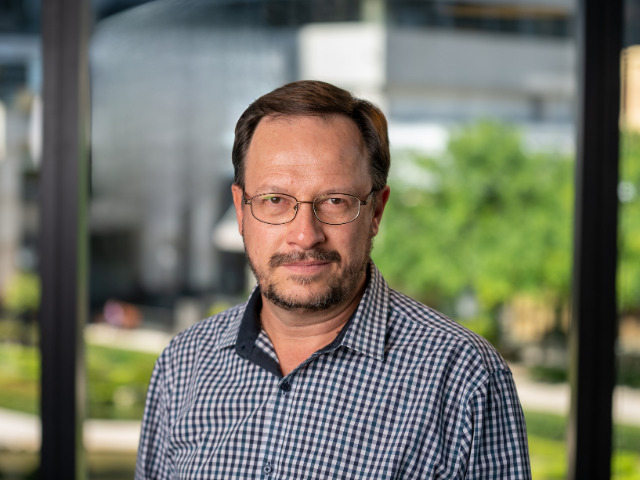
Fanie Van Der Linde has worked on engineering projects around the world, most recently helping clients to manage their tailings storage facilities ‘Down Under’.
From planning and approvals through development and operations into rehabilitation and closure development, Fanie’s 25 plus years of expertise is helping mining clients design and maintain their tailings management programs. Here he shares his insights into the significant challenges facing mining operators to adopt and comply with global reforms to make mines more compliant and environmentally sustainable.
Tailings storage management is a challenging and complex part of mining operations, what is your approach?
How I explain it – I call it the ADC of tailings storage management.
The A stands for annual audits; The D is the design, and The C is the construction monitoring. All three aspects have an important role to play, and in all three aspects Tetra Tech have specialist services which we build into our integrated mining lifecycle model.
In Australia it is tightly regulated, with two regulators overseeing mine tailings. The first is the Department of Water and Environmental Regulation (DWER) and the other is the Department of Mines and Industry Regulations and Safety (DMIRS).
For new tailings development or expansions, approval from both these government departments is required in the design phase – prior to any construction commencing.
All mines must comply with the Australian National Code of Large Dams (ANCOLD). Once the design document is prepared, it’s submitted to both regulators for approval. On approval from both, it is submitted, and we can then move into construction phase.
As consultants, we need to be actively involved in the construction process to oversee the contractor ensuring the construction is done in accordance with the design team.
At the end we issue a Construction Report which incorporates a Certificate of Compliance, photographic evidence, and progress reports on all of our meetings.
Both regulators DMIRS and DWER want a consultant to be involved in an annual auditing process. DMIRS specify that a suitably qualified geotechnical engineering consultancy needs to audit the facility on an annual basis.
Our design report involves stability analysis and monitoring of the embankment. To ensure safety, we need to maintain a factor of safety above the minimum specified in the ANCOLD document. This safety must remain high as we utilise the vibrating wire piezometers (VWP) as instrumentation to measure the phreatic surface in the embankment.
What are some of the challenges mining operators face in the future of tailings management?
The biggest challenge for mining operators around the world is the Global Industry Standard on Tailings Management (GISTM). The guidelines were launched in August 2020 and were developed through an independent process co-convened by the United Nations Environment Programme, Principles for Responsible Investment, and International Council on Mining and Metals.
The guidelines aim to prevent catastrophic failure and enhance the safety of tailing’s storage facilities (TSF) across the globe. It requires operators to take responsibility and prioritise the safety of tailings facilities through all phases of a facility’s lifecycle, including closure and post-closure.
Most of our clients need to adhere to the rules that the GISTM laid down to make tailings management safer for all people globally. Clients who are members of the International Council of Mining and Metallurgy (ICMM) need to adhere to all rules by 2025.
Tetra Tech Coffey brings both technical, scientific, and management consulting expertise to this challenge. We have a broad spectrum of expertise in tailings management, and we are already working with clients to transition to these GISTM compliance and monitoring requirements.
How far along that journey is the Australian industry progressing?
Here in Australia, we are only just getting started and there’s a lot of work to be done.
Maybe 5% have reached compliance, and that’s why consultants are in such high demand. We really need more tailings engineers to enter the industry over the next few decades to meet this demand.
At Tetra Tech we are trying to expand our team, to meet this demand. Tailings have got a bad reputation because of the high complexity. That’s why people might shy away from forging a career in tailings management. There is no doubt that it is a risky business, however, the mining industry on the whole are committed to adhering to global standards and approaches to tailings management. I think it can be a fascinating career for an engineer or environmental scientist to get involved in and make a really positive impact.
How has Tetra Tech Coffey adapted innovative technologies or approaches to meet the needs of our mining clients?
There are several areas where we are adopting technology, either to create efficiencies or safety; tailings facilities can be up to 60 meters high, and/or located in remote areas.
In another area we are using cone penetrometer testing (CPTu) which is appropriate for identifying the key engineering properties of tailings.
Typically, a geotechnical investigation needs to be performed before you move onto the design stage. (CPTu) is a probe that actually pushes through the tailings, gathering data to be analysed. This is where we can see all the different layers of deposited tailings which is usually either sand or clay – it depends on what ore you are processing.
Another challenge is monitoring embankment stability, basically trying to locate any weak points in the TSF embankment because when an embankment fails, it can be disastrous. So, we install instrumentation to aid in monitoring stability of the embankment.
Connect with Fanie at [email protected]