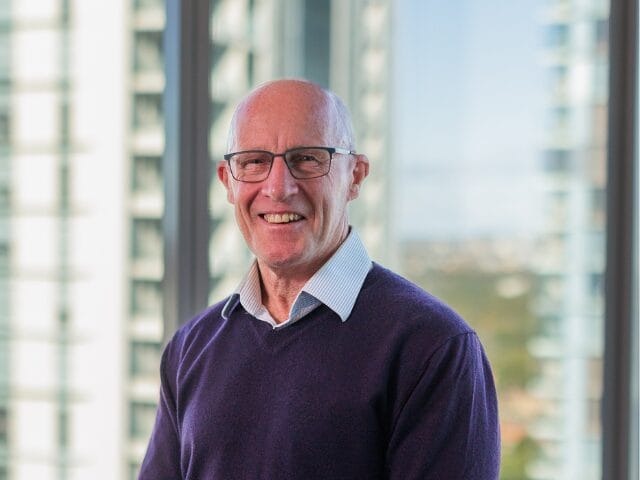
The Penrith Lakes Scheme was a transformative project located adjacent to the Nepean River north of Penrith, NSW, Australia where 1935 hectares of land once used for sand and gravel quarrying was rehabilitated for flood mitigation, public recreation and urban development. From the 1990s through to early 2000s the Sydney International Regatta Centre (SIRC) was built in preparation for the Sydney 2000 Olympics, with the construction of the Regatta Centre the first stage of the site being returned as a parkland and lake system.
Principal Geotechnical Engineer, Robert Tuner was Tetra Tech’s Project Director from 2006 to 2015. Here he outlines the geotechnical challenges to address and remediate the landform for its intended purposes.
Background
The Penrith Lakes Development Corporation (PLDC) was formed in 1980 to oversee the remaining extraction of resources and progressive rehabilitation of the site. Initially several other consultants also serviced the project, but from about 2001, Tetra Tech Coffey (Tetra Tech) was the primary geotechnical consultant for this ambitious landform remediation project.
Broadly, the land had been historically affected by a century of widespread quarrying in 12 separate pits to depths of 12 to 15 m. To quarry the resource, the upper 6m or so of overburden was stripped and redistributed around the site as uncontrolled filling/stockpiles. The first stage of the rehabilitation scheme (completed in the 1990s) involved constructing the Sydney International Regatta Centre (in the southern quarter of the site) for the Sydney 2000 Olympics.
In the early 2000s, landform remediation for the flood mitigation scheme and parkland development commenced. This would eventually involve construction of more than 100 million cubic metres of Engineered Fill. At this time, The PLDC began to examine the prospect of including suburban development (Urban Land) within the remediated landforms.
What were the broad goals and objectives of the Project?
Tetra Tech worked with PLDC its team of specialist consultants to achieve the following outcomes:
- Environmental Remediation: Identifying and remediating contaminants from mining activities and re-establishing natural habitats.
- Landscape Design: Regrading the land to achieve flood mitigation objectives, while also creating usable, aesthetically pleasing, and safe topography.
- Geotechnical Stability: Achieving ground stability through various ground improvement techniques (dynamic compaction, impact rolling, conventional engineered fill construction, preloading and surcharging).
- Infrastructure Development: Building or upgrading roads and transportation links and ensuring the provision of necessary utilities.
- Regulatory Compliance: Navigating the complex process of obtaining necessary permits and approvals from local, state, and federal authorities.
- Community and Stakeholder Engagement: Addressing concerns of local communities and stakeholders and keeping all parties informed.
Achieving these outcomes required careful planning, specialist knowledge, application of intelligent risk, and a willingness to collaborate with and trust the various stakeholders.
What geotechnical challenges did the redevelopment face?
After extraction of the sand and gravel resource, the site comprised vast areas and depth of stripped overburden dumped or spread as uncontrolled fill. At various locations, there were large recent and relic tailings ponds with unconsolidated sediments.
To create landforms that would remain stable and sustainable in their post-construction function (i.e. lake shorelines, parkland and urban lands) through episodes of periodic flooding, it would be preferable to reconstruct the landforms wholly as controlled fill. However, the logistics and costs associated with that scale of reclamation were prohibitive. Subsequently, alternative ground improvement methods were trialled, such as dynamic compaction and impact rolling, and incorporated into the landform construction in some areas. These methods, however, were not able to compact the uncontrolled fill to its full depth.
Consequently, landforms design options that incorporated controlled fill (or dynamically compacted fill) constructed over uncontrolled fill were investigated. This was especially challenging in urban landforms because these could tolerate significantly less settlement than other landform functions.
The danger with this type of landform construction is that the land would be constructed “in the dry”. Later, when water is introduced to the lake basins, the uncontrolled fill at the base of the landform would become saturated and may collapse, causing large settlements at ground surface level.
PLDC’s design brief was that urban landforms should be capable of supporting footing systems that were consistent with certain standard footing system designs stipulated in AS2870 “Residential Slabs and Footing”. This requirement was especially challenging because those footing systems are designed for failure mechanism caused by ground movements that are entirely different than those that would be mobilised at Penrith Lakes.
How did innovation play a part in Tetra Tech’s solution?
Residential footing systems are typically designed to tolerate differential ground movements arising from seasonal shrink/swell movements in the near-surface soil profile due to soil reactivity. At Penrith Lakes, houses may experience differential ground movements arising from compression and creep settlements and hydro-compression (collapse) settlements due to future groundwater level rises in the landform.
Each of these settlement mechanisms were examined to estimate the cumulative differential settlement that may occur across a house footprint. For collapse settlement, we assessed the likely maximum void that could be created (through hydro-compression) at depth in the landform. We then applied “tunnel theory” to assess the surface deflections arising from the void formation at different positions beneath the house footprint.
The design objective was to determine what thickness of controlled fill needed to be placed over the lower uncontrolled fill to limit ground surface movements arising from the various settlement mechanisms to those that could be accommodated by a specific footing system defined in AS 2870.
To my knowledge, this was the first time that such an approach had been adopted for this scale of development. The advantage of working with a consultant like Tetra Tech is that we have access to a team of leading minds with years of experience. For this aspect of the project, I worked with my colleague Prof Harry Poulos, one of the world’s pre-eminent geotechnical experts.
Summary
The Penrith Lakes Scheme aims to transform the site into a sustainable and vibrant community space, providing long-term benefits such as recreational areas, residential zones, and restored natural habitats. The redevelopment also ensures that the land can adapt to changing needs and conditions in the future.
The transformation of Penrith Lakes from a historical quarry to a parkland and urban haven showcases the potential of disciplined geotechnical planning combined with innovative remediation techniques. Tetra Tech Coffey and PLDC have set the stage for a sustainable and vibrant community space, highlighting the importance of careful planning and collaboration in redeveloping quarry sites.
For more information, connect with Rob Turner at [email protected]